With the expected increase in use of plant growth regulators such as dicamba-based products (XtendiMax®, Engenia®, and FeXapan®) and the recent addition of 2,4-D choline as part of Enlist technology, sprayer cleanout will be more important than ever before. In addition, the expected introduction of new seed traits (e.g., Balance Bean/GT®, MGI) will continue to make sprayer system cleanout an important management focus in order to reduce potential for injury of subsequent crops.
It is not possible to remove all of the dicamba or 2,4-D residues from a sprayer with only water. Furthermore, herbicides can form deposits in the sprayer tank, screens, filters, nozzles, at the end caps or within other portions of the plumbing system. If the next sprayer load is Roundup or Liberty herbicide, the surfactants from those products can act like a powerful tank cleaner, reacting with plant growth regulator (PGR) residues and creating a byproduct that can injure sensitive crops (e.g., non-dicamba tolerant [DT] soybeans).
Figure 1 shows herbicide residue buildup at the end cap on a row crop sprayer that had not been properly cleaned multiple times. This would be a significant problem with PGR residues.
Applicators need to make sure that tanks, including the boom assembly, are cleaned. Stainless steel wet booms with end caps are easier to clean and flush than dry booms. Dry booms with their hose and nozzle assemblies are more subject to be contaminated compared to stainless steel tubing or pipe. There are more places for herbicide particles or residues to bind with a dry boom setup. For more information see the NebGuide Spray Boom Set-up on Field Sprayers” (G2091) or the 2018 Guide for Weed, Disease, and Insect Management in Nebraska (EC130).
How much dicamba spray solution does it take to cause visible injury to susceptible soybeans either at the 22 ounce rate of XtendiMax or FeXapan or the 12.8 ounce rate of Engenia when left in a 1,000 gallon tank or other sprayer components?
- At 10 GPA spray rate – 64 ounces (1/2 gallon)
- At 15 GPA spray rate – 96 ounces (3/4 gallon)
- At 20 GPA spray rate – 128 ounces (1 gallon)
Related Stories
- Potential Off-Target Dicamba Movement from Corn Applications
- Can We Manage Applications Dicamba in 2018
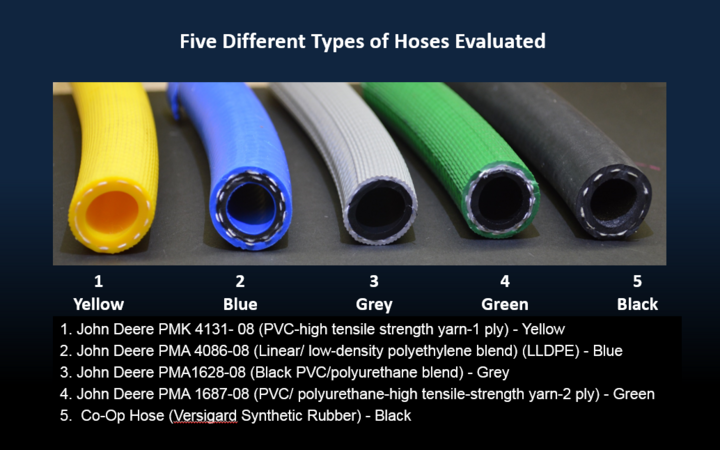
In addition, the type of hose used for dry booms can influence the level of dicamba residues. Oil-resistant hoses in general are less of a problem and usually higher quality. Research by Dan Reynolds , a weed science professor at Mississippi State University, studied five hose types and found a difference in how well they could be cleaned. See Figure 2.
Each hose type was exposed to dicamba multiple times, then 1) flushed with water alone, 2) flushed with water plus ammonia, or 3) not cleaned with additional water. Afterward, the hoses were carefully examined for dicamba residue. The blue polyethylene-jacketed hose had less than 1 ppm residual concentration of dicamba when flushed with water alone or water plus ammonia. The blue hose also had a lower concentration of dicamba with no additional flushing with water alone compared to the other hose types. When cutting the hoses apart and inspecting the interior lining with an electron microscope, Reynolds discovered tears and cavities that could sequester herbicide and become hard to clean (Figures 3 and 4).
The low density, blue polyethylene blend hose (LLDPE), after being used eight times had a smooth interior surface when examined by the microscope (Figure 5). It retained the least amount of dicamba whether flushed or not, and it was the most expensive hose, manufactured for John Deere, Canada. For additional information on the blue hose, go to https://go.unl.edu/jdblue.
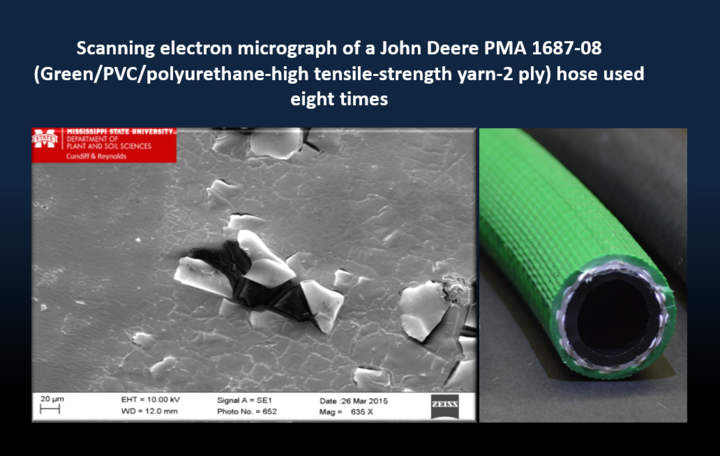
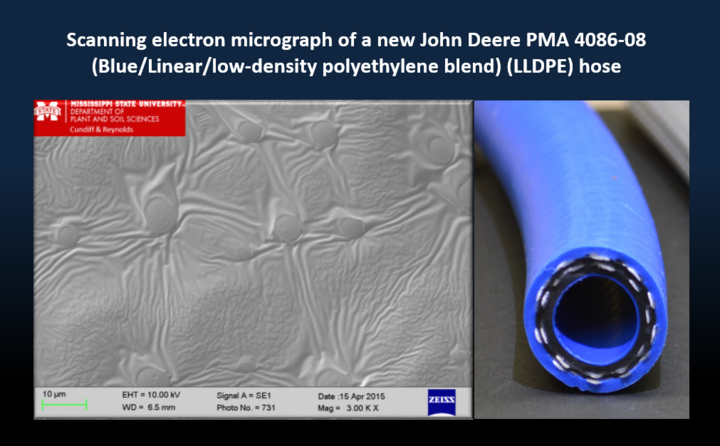
Cleaning the Sprayer
Based on the label requirements for Restricted Use Pesticides (RUP), applicators must ensure their spray equipment is clean both before and after applying a dicamba product. Cleaning equipment prior to loading with dicamba assures that nothing left in the sprayer would negatively impact the performance of the dicamba or the crop being treated.
The RUP dicamba labels require spray systems to be cleaned, following the procedures listed on the RUP dicamba labels, before using the herbicide after another type of spray mix, and immediately after using dicamba before switching tank mixes. This is critical in order 1) to avoid contaminating the RUP dicamba spray mix with other chemicals that might promote the volatility of dicamba and 2) to avoid carrying dicamba over to a sensitive crop in the next load or application.
Note: The Nebraska Department of Agriculture (NDA) also advises applicators that all transportation equipment hauling pre-blended dicamba loads to the field are also potential sources of contamination and should be treated the same as spray equipment when it comes to cleaning before changing product mixes.
How much is adequate rinse water in the field with a modern sprayer?
"How much water should you flush through sprayers in the field? A general rule of thumb is to use 10 percent of the tank’s capacity per rinse," writes Fred Whitford and his co-authors in Removing Herbicide Residues from Agricultural Application Equipment - How Proper Cleaning Helps Prevent Crop Damage and Improves Performance, a publication of Purdue University Pesticide Programs.
"Another general rule says to add at least two to three times the amount of gallons applied per acre. Each rinse of the boom will range from 30 to 50 gallons of water. For example, if a spray application used 15 gallons per acre, 30 to 50 gallons should be sufficient to flush the sprayer. Add more water if the spray coming out of the nozzles during the flush process doesn’t look clean. Some applicators drain as much product as possible out of tanks before circulating clean water. They will open the main valves to drain the tanks and hoses. They will put in 3 to 5 gallons of clean water and recirculate to get the remaining material out of the tank by reopening the tank valve. This tactic will make the first rinse a cleaner rinse, because the water is circulated between pump and tank."
Preliminary research suggests that rinsing three times with adequate water is more important than the type of detergent used for a commercial tank cleaner on the second rinse. Only use a cleaner recommended by the label and/or manufacturer.
The only absolute way to avoid tank contamination with plant growth regulators (PGR) is to have a sprayer dedicated to PGR applications. If this is not an option, a thorough cleaning for the required time with the proper tank cleaner and adequate water is crucial. NEVER mix ammonia and chlorine beach; their solution will produce a toxic chloramine gas, which is a health hazard to the applicator.
Have a plan to eliminate PGR residues from tender or nurse trucks as well. There have been examples where “hot loads” from an uncleaned nurse tank were supplied to the field sprayer, contaminating a clean sprayer. Outside sources of contamination also can come from shuttles and minibulks (not recommended to be reused), induction cones, tank-fill hoses, tires on sprayers with front mount booms, and nurse tanks supplying hot loads.
Step-by-Step Procedure to Clean Dicamba Out of a Sprayer
The following sprayer cleanout procedure is required by the new RUP dicamba labels. Always read and follow label guidelines.
1. After last load, drain sprayer immediately (including boom and lines). Do not allow spray solution to remain in the spray boom lines overnight or for extended periods of time prior to flushing.
2. Flush tank, hoses, boom and nozzles with clean water. Open boom ends and flush if so equipped.
3. Inspect and clean all strainers, screens, and filters.
4. With cleaning solution containing a strong detergent recommended by equipment manufacturer, mix enough solution to wash entire spray system inside and out, including the inside of top surface. Start spray tank agitation system and thoroughly recirculate cleaning solution for at least 15 minutes. All visible deposits must be removed from the spraying system.
5. Wash all parts of the tank, including the inside top surface. All visible deposits must be removed from the spray system.
6. Flush hoses, spray lines, and nozzles with cleaning solution for at least 1 minute.
7. Remove nozzles, screens and strainers and clean them separately in cleaning solution after completing the above procedures.
8. Drain pump, filters, and lines.
9. Rinse the interior AND exterior of the entire spray system, including the boom, with clean water.
10. Appropriately dispose of all rinse water at the field (target site) or on a load-out pad designed to capture and reuse the solution as makeup water in the next load of dicamba.
Take-Home
These examples illustrate the many ways a load can become contaminated; therefore, it is critical to maintain your sprayer dicamba-free, which can be a tricky task.
Resources
A Purdue University publication is an excellent resource for cleaning sprayers: Removing Herbicide Residues from Agricultural Application Equipment - How Proper Cleaning Helps Prevent Crop Damage and Improves Performance (PPP-108). After reviewing the publication one applicator said “I am going to have my operators read through this and together we are going to put together our own checklist per machine.”
Cleaning Pesticide Application Equipment, Nebraska Extension Nebguide G1770
Cleaning Field Sprayers to Avoid Crop Injury, University of Missouri publication G4852