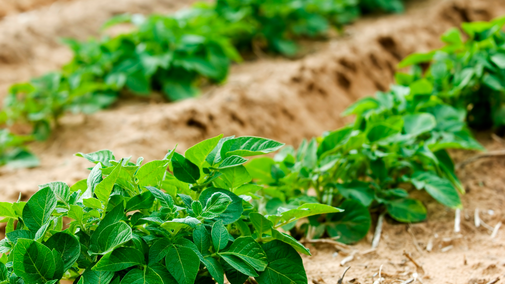
Nebraska Potato Production
Nebraska ranks 10th for potato production in the U.S. In 2023, growing mainly white and russet potatoes, with a small percentage of red and yellow varieties. Nebraska's potato production hit a record high at 11.0 million cwt and 21,900 acres harvested, resulting in $139 million, according to USDA National Agricultural Statistics Service.
Contact:
Dipak Santra
Alternative Crops Specialist
(308) 632-1230
dsantra2@unl.edu
Faculty Bio
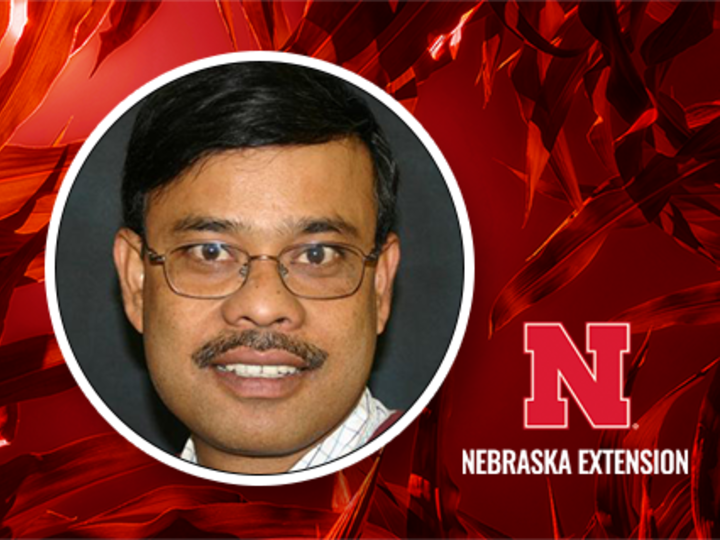
Potato Production Resources
Key Production Stages
Scheduling Key Practices
Characterization of potato growth and development is important for the scheduling of production practices, yield prediction and hail loss insurance. Most past descriptions emphasize vine growth above-ground and neglect the below-ground tubers (Anonymous, 1976; Sparks, 1972; Sparks and Woodbury, 1959). Recently, growth stages have been described integrating both vine and tuber growth and relating some agronomic practices to them (Bishop et al., 1986; Bissonnette et al., 1993; Rowe, 1993). This section (based on Pavlista, 1995) describes stages of potato production and indicates key practices at each stage. Norgold Russet, an early season potato, grown in Scottsbluff, Nebraska, was used as a model to depict planting on May 10 and subsequent plant development occurring chronologically in a desired production situation (see "Model Systems"). For each stage or time period, key production practices and potato development events are described in the order shown in Table 1. For pest descriptions, fertilizer suggestions, and variety requirements, see appropriate panels in this web-site.
I. PRE-PLANTING
Most Critical Actions = seed handling and preparation, fertilization.
Key Biological Activities = seed ageing and dormancy.
Production Practice
Starter fertilizer may be applied prior to planting. A dry N-P-K (nitrogen-phosphorous-potassium) fertilizer mixture (18-46-0 is commonly used in Nebraska) may be broadcast and disced into the soil before planting. If used in home gardening, application at planting is recommended. Gardeners can break the ground up with a hoe or shovel just prior to planting or have the area be garden plowed. Pre-irrigation may be used to eliminate soil clods for ease of planting. A soil moisture of 70 to 80% field capacity (3,10) is considered ideal for most soils.
Seed-Cutting Practices
During this period the main concern is to prepare the seed pieces for planting and avoid seed decay by diseases. In the USA, potatoes are not produced from true seeds but from tubers harvested from the previous crop. Nearly all production is from "seed pieces" cut from larger "seed-certified" tubers; some production is from "single drops" which are small whole tubers. Gardeners might want to use single drop seed if available and avoid some of the seed preparations otherwise recommended. All seed pieces should be about 2 ounces in weight (6 to 10 even-sized seed pieces per pound of whole potato tubers). Those less than 1½ ounces should be discarded. Since seed tubers are stored at 36-40 degrees F, they need to be warmed before planting. When a 40-degree F seed piece is planted in 50 degrees F and wet soil, moisture will condense on the surface of the piece, creating an environment highly favorable for disease development. Cut seed pieces need to be warmed slowly and kept ventilated to allow for wound healing, which is the formation of a protective layer, called the suberin layer, over the cut surface.
At the time of cutting, seed pieces should be treated with a fungicide dust. This aids in drying the cut surface and gives the seed pieces some protection against decay by micro-organisms. Commercial growers using mechanical cutters need to disinfect the cutting blades between each lot of seed-tuber to protect against carryover of disease organisms from one lot to another. Homeowners who hand-cut seed, can dip a knife into a 10% clorox solution between cutting washed tubers. Note that dirt can inactivate the bleach so the solution should be changed often (Rowe, 1993).
Plant Development
During storage, seed tubers harvested the previous season were dormant. Toward the end of the storage period, dormancy usually ends and, to varying degrees, sprouting may begin. The tuber is the sole source of water and nutrition for the sprouts and the life activities within the tuber. Performance of seed pieces is greatly influenced by the tuber's physiological age which is affected by time, handling and storage conditions. Bruised seed tubers are physiologically older than non-bruised ones. Plants grown from seed pieces cut from physiologically older tubers tend to emerge faster, have more stems, grow smaller vines, have more tubers per plant, bulk tubers quicker, die faster, and yield less. Seed that is not aged excessively is preferred.
References
- Anonymous. 1976. Potato loss instructions. National Crop Insurance Assoc. Bull. #6453.
- Bishop, G.W., G.D. Kleinschmidt, K.W. Knutson, A.R. Mosley, R.E. Thornton, and R.E. Voss (Technical Coordinators). 1986. Integrated pest management for potatoes in the western United States. Univ. California Agric. Nat. Resources Bull. #3316.
- Pavlista, A.D. 1995. Potato Production Stages: Scheduling Key Practices. Univ. Nebraska Coop. Extension Circ. #95-1249.
- Rowe, R.C. (Editor). 1993. Potato Health Management. Publ. The American Phytopathological Society Press, St. Paul, MN.
- Sparks, W.C. 1972. An aid for determining stage of potato plant growth. Univ. Idaho Current Information Ser. #186.
- Sparks, W.C. and G.W. Woodbury. 1959. Stages of potato plant growth. Univ. Idaho Agric. Exp. Sta. Bull. #309.
Planting to Emergence
The planting to emergence period usually ends at 3 weeks after planting and is lengthened by cooler soil conditions; it ends when sprouts emerge from the soil surface.
Most Critical Actions = weed control and fertilization.
Key Biological Activities = root, sprout and rhizome growth.
Production Practices
Seed pieces should be planted six to eight inches deep. Do not plant seed pieces in soil with a temperature less than 50oF. Soil moisture in the top foot should be between 65 and 80% field capacity. Irrigation during this period, i.e., "irrigating the plants up," is not recommended. There is enough moisture and nutrition in a healthy and acceptably-sized (1½-2 oz) seed piece to sustain the plant to emergence. Also, irrigation during this planting to tuber initiation may promote seed decay before emergence and early dying (Verticillium wilt) later when the tubers are rapidly enlarging.
Fertilization can be applied successfully during this period. Nitrogen, phosphorus and potassium (N-P-K) can be added as a side-dress two inches beside and at the same depth as the seed pieces. Row spacing is usually between 32 and 36 inches, the latter being most common. Recommended plant spacing within the rows varies with the intended market and variety; narrower spacing as low as 6 inches for seed tuber production and further apart as much as 16 inches for "bakers" and long french fries.
Pest Control
A systemic insecticide may be added into the furrow during the planting operation by commercial growers, but home gardeners should use foliar insecticide as needed during the season. In-furrow application involves placing the material after the furrow-opener and before seed piece placement. When properly done, some soil will cover the material before the piece falls due to the motion and vibration of the planter.
Pre-emergence herbicide application is the most critical pest control operation during this period. Most potato herbicides are labelled for pre-emergence application and are not recommended for post-emergence use on many potato varieties, especially white-skinned varieties, because these may be injured by the herbicide. Most pre-emergent herbicides used in potatoes have a six to eight week active residual period in the soil. When applied at recommended rates between one to two weeks after planting, they will suppress weed growth until five to seven weeks after emergence. By then, healthy plants should have closed the rows and the potato plants themselves will keep down any newly emerged weeds by shading them. Cultivation is also used during this period as a mechanical weed control practice. By itself, however, cultivation will have little residual effect and weeds will appear until row closure. Also note that after some pre-emergent herbicide applications, cultivation would have a negative impact by breaking the herbicide layer and throwing treated soil against the newly emerged plants. The use of herbicides by home gardeners is not recommended due to sensitive garden plants grown nearby, the small areas treated and possible exposure of pets and children. In this case, the operative phrase is "a-hoeing we will go."
Plant Development
The seed piece itself is its own principle source of food and water during this period, and must be healthy from the start. After planting, the seed piece will sprout and grow toward the surface. Usually, more than one sprout will grow from a seed piece and often more than one stem will appear from a sprout. The additional stems from a sprout are actually branches.
During this period, plant resources are devoted to root and shoot growth and will reach 18 inches in length on the average, some varieties longer. Potato roots tend to be relatively shallow. Rhizomes, or stolons as they are commonly but erroneously called, do not appear until around emergence. Rhizomes are the structures on which the next generation, the daughter tubers, will form.
Emergence to Tuber Initiation
The key characteristics of this stage are rapid vine growth, continued root growth and tuber initiation (enlargement at the ends of rhizomes). This growth stage covers from emergence to pre-bloom, the period from 3 weeks after planting (emergence) to 6 weeks after planting (or 3 weeks after emergence) for a short-season variety such as Norgold Russet. This period is similar for mid-season varieties but longer for long-season ones.
Most Critical Actions = disease and insect monitoring for treatment, gradually increasing irrigation and second application of nitrogen.
Key Biological Activities = healthy and rapid vine growth, root growth and development of tubers on the rhizomes.
Production Practices
Soil moisture should be at least 65% field capacity; 70 to 80% is preferred. Therefore, irrigation can be kept infrequent in the beginning and intensified as the plants get larger. Additional application(s) of fertilizer, primarily nitrogen, are made during this period.
In the early part of this stage, cultivation and hilling can be done. Remember cultivation or hilling after placement of certain pre-emergent herbicides may interfere with their weed control activity and may injure the plants. Care must be taken to avoid root pruning. Remember the roots are in the soil at the side of the hills and between the rows.
Pest Control
The use of certain herbicides labelled for early post-emergence application at this stage is not generally recommended due to possible injury to the plants. This caution depends on the varietal sensitivity to these materials which is not known for all varieties. There is minimal use of fungicides and insecticides under the Nebraska climate. On the East Coast and in Southern states where high humidities and warm night temperatures are common, applications of these materials is important at this stage to avoid plant damage.
Plant Development
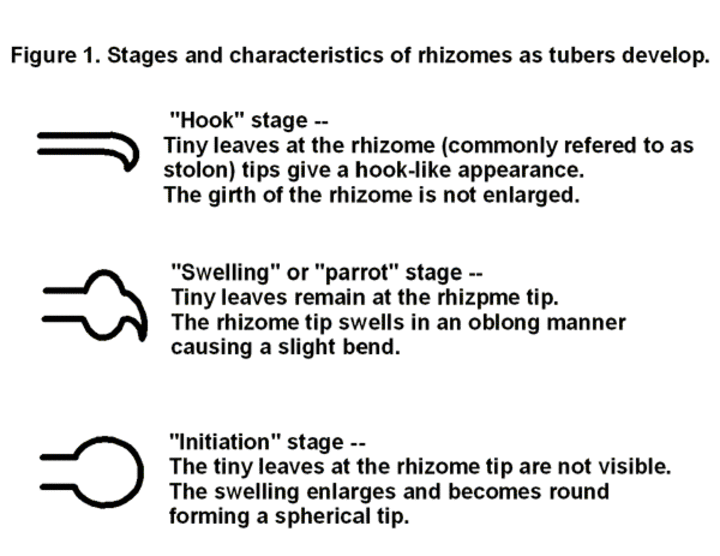
The major characteristic of this stage is rapid vine growth; the canopy may double in height every week for the first three weeks. Although the seed piece is still a key food source in the beginning of this stage, as the foliage develops and grows, food production (photosynthesis) increases until the leaves become the only food source.
Rhizomes are underground branches; when exposed to light, they will turn green, form leaves and secondary branches. From 3 to 6 weeks after planting, the rhizomes are in the "hook" stage (Figure 1A) which is characterized by tiny leaves at the end of the rhizome forming a hook-like appearance. From the hook stage, the rhizomes will go into the "swelling" stage which is characterized by an oblong swelling that forms behind the hook and a slight "bowing" of the tip into what looks like a "parrot" profile (Figure 1B). From the swelling stage, the rhizomes initiate tubers.
The duration from planting to tuberization depends on planting date, variety, temperature, quality of seed piece, and nitrogen fertilization.
Tuber Initiation to Full Bloom and Tuber Bulking
As the name implies, tubers form at this stage. Tuber initiation covers the period from the rounding of the ends of rhizomes into spheroids and the appearance of the first flowers (in most varieties) to full bloom and the start of tuber bulking, lag phase of tuber growth. For short-season varieties, this period is from 6 to 8 weeks after planting (3 to 5 weeks after emergence).
Most Critical Actions = irrigation, and pest monitoring and early control.
Key Biological Activities = initiation of tubers and row closure.
Production Practices
Irrigation becomes increasingly important during tuber initiation due to high rates of transpiration (water movement within plant) and may aid in common scab control. Optimum soil moisture is 80 to 90% field capacity. Fertilizer is not applied during the rest of the season except by commercial growers. These growers may use petiole-nitrate analysis to indicate whether nitrogen levels in the plant have fallen below that suggested for the variety being grown. Nitrogen, if required, needs to be added in small amounts through the irrigation system to maintain tuber quality. Note that excess nitrogen at this stage may inhibit tuber initiation and could leach into the ground water.
Pest Control
Herbicide residual activity should carry to the end of this stage when the rows close (that is, when plants in adjacent rows touch each other between the rows across the furrows). In comparison to many other potato production areas, foliar application of fungicides and insecticides is usually low in Nebraska. However, this may vary widely based on the intended market; for instance, growing seed potatoes requires higher pesticide input than growing tablestock. Also, pesticide use greatly varies from year to year depending on weather conditions during and prior to the growing season, such as winds from the Gulf of Mexico bringing in leafhoppers and aphids. In areas with high humidity and warm night temperatures, disease and insect problems are much more severe and occur earlier than in Nebraska. The cold winters (-30 to -40 degrees F), little snow cover and arid climate in Nebraska help to keep pest populations low.
Plant Development
This stage is identified by the formation of tubers at the end of the rhizomes. Tubers are initiated when the tiny leaves at the end of the rhizome disappear and the tip becomes oval ("egg-shaped") or spherical ("ball-shaped") (Figure 1C). The tubers although formed grow very little for a couple of weeks while the vines continue to grow.
Toward the end of this stage, vine growth slows and the plant is in full bloom. Varieties differ in the amount of flowering. Most varieties are determinate and thus vine growth ends with flowering. However, some long-season varieties are indeterminate and vines continue to grow after flowering. The most notable example of the latter type of potato is the Russet Burbank. Note that flowers may be pollinated and produce small, round, green fruit containing true seed. Row closure occurs during this stage assuming healthy vine growth. This stage is a transition from a time of vine growth to a period of tuber growth or bulking.
Tuber Bulking to Plant Senescence
This usually is the longest stage in potato growth, covering from full bloom to senescence or vine death in determinate varieties. It extends from 8 to 14 weeks after planting (5 to 11 weeks after emergence) for early-season varieties and is longer for later season varieties.
Most Critical Actions = irrigation, pest control and stress avoidance.
Key Biological Activities = tuber growth.
Production Practices
The most important practice in this stage is irrigation because the plant has its highest demand for water at this time. Depending on rainfall, application of 1½ inches per week is normal or a total of 12 to 15 inches of water is applied during this stage. Soil moisture needs to be kept between 80 and 90% field capacity. Avoiding plant stress is critical. In hot, dry climates, sprinkler irrigation also may help to cool the plants and soil.
Pest Control
The key is to keep plants from being stressed. In many potato production areas, fungicides are applied to prevent early and late blight. In Nebraska, late blight occurs seldom, once every 10 to 15 years, and early blight usually occurs toward the end of the season. A pre-harvest treatment of certain fungicides will reduce tuber break down in storage due to leak and other diseases. Irrigation may help minimize tuber blemishes due to common scab and black scurf. Sulfur can be applied through sprinkler irrigation to assist healing of vines after hail or when early blight is present. Diseases such as early dying, wilts, and black leg cannot be chemically controlled but using certified seed and keeping the plants healthy usually will prevent them from being a problem.
The use of foliar-applied insecticides depends on insect populations. Often in Nebraska, an insecticide is applied only once during the middle or latter part of the season. Natural predators in Nebraska often keep the population of the Colorado potato beetle below injurious levels. And, the occasional migration of the potato leafhopper and green peach aphid (once in 4 to 5 years depending on the wind from the Gulf of Mexico) occurs relatively late in the season. Insect control is primarily important to the potato seed producer in Nebraska because of their potential for carrying plant viruses.
Weeds are not usually a problem after row closure. There are few herbicides available for post-emergence use on potatoes.
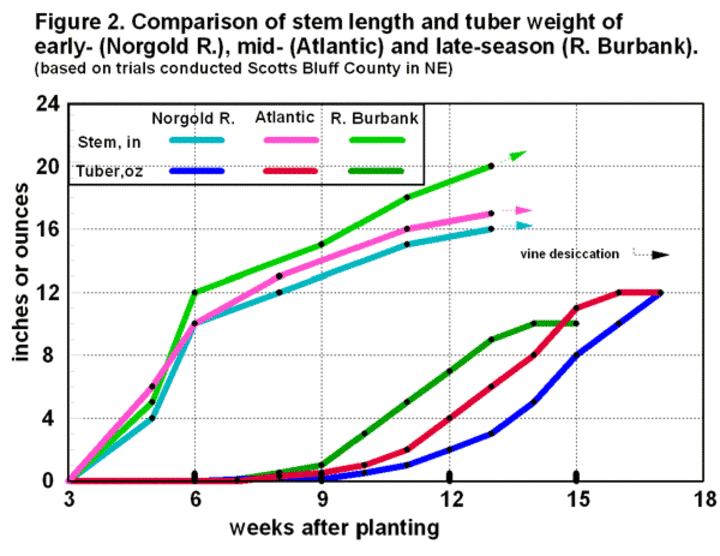
Plant Development
Growth during this stage is totally centered on the tubers and final yield and quality depends on what happens here. The tubers will undergo a logarithmic growth pattern (Figure 2) which is characterized by a gradual growth increase, then a near doubling in size and weight and ending with a gradual slowing down of growth to a plateau level. During this period, the tubers are the food sink; sugars are transported from the leaves to the tubers and converted to starch. The transport of sugars in the reverse direction can occur if plants are under stress which may result in lower yields and poorer market quality. All plant stress should be avoided and so all steps should be taken to "keep them happy." Except for indeterminate varieties, there should be no or little vine growth. Vine growth will consume nutrients at the expense of tuber growth.
Plant Senescence to Harvest
The two facets of this stage are vine and tuber maturation. It begins with vines showing the first signs of dying, yellowing of leaf tissue, until harvest. In early-season varieties, this covers from 14 to 18 weeks after planting (11 to 15 weeks after emergence). For later varieties, this stage can come later and last longer.
Most Critical Actions = vine desiccation.
Key Biological Activities = vine death and tuber maturity.
Production Practices
Little, if any, irrigation is needed during this stage; the soil moisture should be held between 60 and 65% field capacity, mostly to avoid clumping for easier harvest. No fertilization should be applied; it may delay vine maturation and make desiccation more difficult.
The main practice in this stage is the use of desiccation techniques to hasten vine death. These can be chemical, mechanical or a combination of the two. The main purposes of desiccation are to promote tuber maturity, ease harvesting and minimize tuber infection by blight spores on the vines.
Plant Development
From senescence to death, the leaves and branches turn yellow to brown and the leaves fall off.
From senescence to death to harvest, the tubers mature; their growth ends. Dry matter, especially starch, reaches a peak and the reducing sugars, specifically glucose, fructose and sucrose, decrease to a low. The tuber skin hardens and thickens. These changes are promoted by vine death. Chemical vine desiccants are used to achieve complete and yet gradual (two to three weeks) death of vines. If death is too rapid either by desiccation methods or frost than the tubers do not mature as well and may develop internal defects.
Harvest and Storage
After these production stages are done, the tubers need to be removed from the ground; if not marketed directly following harvest, they need to be stored.
Most Critical Actions = bruise avoidance and storing tubers under the right conditions for their intended market.
Key Biological Activities = bruise healing, tuber dormancy, starch breakdown and metabolism.
Tuber Bruising
A key concern in harvesting potatoes is tuber bruising. The types of bruises are cuts made by the harvester, shatter bruise and internal black spot which develop from dropping tubers or impacting them against each other with force, and skinning resulting from rubbing of the tubers (Kleinschmidt and Thornton, 1991). An additional type, pressure bruise, can occur from piling tubers too high in storage. The severity of bruising is related to the maturity, temperature and hydration level of the tubers. Bruises will lead to several problems in storage. Cuts and shatter are good entry points for diseases. All bruises will speed the aging of tubers and are related to the performance of seed. Internal black spot and pressure will discolor during cooking. Skinning will make an unattractive tablestock potato. Current research is uncovering more and more negative effects resulting from bruising.
Storage Practices
Storage conditions are critical. Appropriate conditions vary depending on the intended market for the harvested potatoes. Conditions such as temperature, curing and sprout control treatment may differ for potatoes to be marketed as seed or tablestock, and for those to be processed into potato chips or frozen potato products (Pavlista and Ojala, 1996). Storage should be well ventilated to promote wound healing and inhibit condensation. Tubers are alive; they respire, take in oxygen and release carbon dioxide. Relative humidity should be about 95% to reduce tuber weight loss, but condensation needs to be avoided to minimize diseases. Potatoes to be sold for seed and tablestock are usually stored at 36 to 40 degrees F; those to be used for frozen, pre-cooked, products are usually stored at 45 degrees F. Those to be processed into potato chips are stored at 50 degrees F to keep reducing sugars from accumulating in the tubers which lead to darkening (Pavlista and Ojala, 1996). For the chip and fry processing markets, and for some long-term tablestock storage, tubers are quite often treated with sprout inhibitors. Of course, these materials cannot be used on seed potatoes. For early planting of seed, sprout promoters are sometimes used. A fungicide may be applied on tubers going into storage to inhibit dry rot.
Plant Development
The tubers are dormant, that is, they will not sprout for some months under storage. However, they are very much alive! When stored at higher temperatures (above 45 degrees F), the dormancy period is shortened and, for that reason, processing potatoes are treated with sprout inhibitors. At colder temperatures such as for seed, dormancy is extended and sprouting is delayed. Sugars accumulate in potatoes under cold storage since tubers do not burn-off (metabolize, respire) the sugars as rapidly as under warmer conditions. Warm storage temperatures favor disease development in addition to sprouting.
References
- Kleinschmidt, G. and M. Thornton. 1991. Bruise-free potatoes: Our goal. Univ. Idaho Coop. Extension Bull. #725.
- Pavlista, A.D. and O.C. Ojala. 1995. Potatoes: Chip and french fry processing. In D. Smith (Ed.), Processing fruits and vegetables: Science and technology. Volume IV: Vegetables: Major processed products (in press). Technomics Publ. Co. Inc., Lancaster, PA.
Model System Comparisons
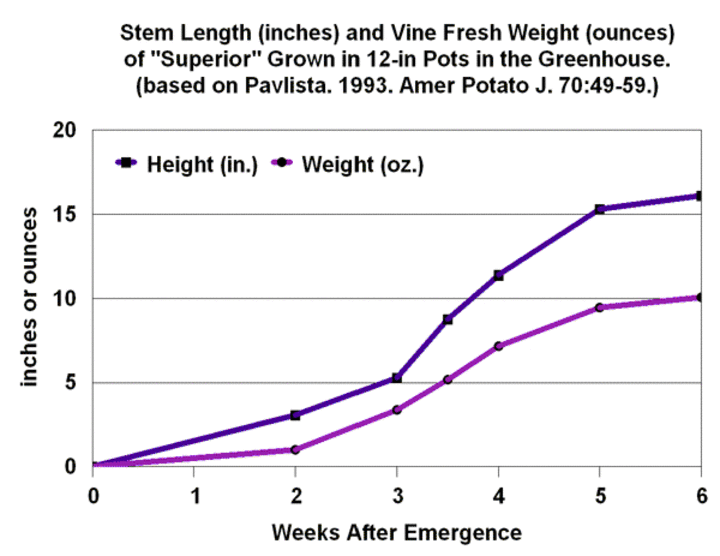
Norgold Russet, a short-season russet-skinned variety grown in the panhandle of Nebraska, is the model depicted in the time-line presented here (Table 1). The growth of the stem and tuber of this variety are shown in Figure 2.
A comparison of this early-russet model is made with Atlantic, a mid-season white variety, and Russet Burbank, an indeterminate, long-season russet variety (Figure 2). Data were collected from russet varieties (Norgold Russet, Russet Norkotah, Russet Burbank, Hilite Russet, and Krantz), white varieties (Atlantic, Monona, Norchip, Snowden, and Wischip), and red varieties (Red Cloud, Red LaSoda and Red Norland). These varieties and their relative performance in Nebraska is described in Pavlista et al, 1992.
Potato varieties show similar growth patterns. That of the variety Superior, a short to mid-season white variety, as grown in a greenhouse is shown in Figure 3 (Pavlista, 1993). Note that vine growth dominates during the first half of the season and that tuber growth dominates in the second half. The basic logarithmic growth of the Norgold Russet variety is typical for a white-skinned mid-season variety such as Atlantic (Figure 2). Long-season, indeterminate varieties such as Russet Burbank show a continuous vine growth until cold weather or vine desiccation. The tuber growth still shows a similar pattern although later in the season (Figure 2).
References
- Pavlista, A.D. 1993. Morphological changes and yield enhancement of Superior potatoes by AC 243,654. Am Potato J 70:49-59.
- Pavlista, A.D., L.E. Williams and C.S. Gall. 1992. Nebraska potato cultivar tests: 1989-1991. Univ. Nebraska Coop. Extension Circ. #92-1247.
Summary of Potato Production Stages
Vine Dessication Why and When
Why Vine Desiccate? When to Vine Kill?
Natural vine desiccation occurs when plants die because the variety is determinate, that is, it is genetically programmed to do so after a length of time. Determinate varieties tend to be short to mid-season varieties but can be long or full-season ones as well. Branching in these varieties ends with flower formation. Indeterminate varieties such as Russet Burbanks tend to continue branching after flowering even thought at a slower growth rate. Environmentally-induced vine desiccation is caused by a change in the weather, primarily cold temperatures as fall progresses. A night freeze will induce dying of leaves and then the whole plant. However, this may not occur until mid to late autumn (October and November).
If plants will die eventually either due to age or cold, why desiccate them mechanically and/or chemically? There are two primary reasons: eliminate vines and enhance tuber maturation.
Eliminate Vines
Eliminating vines either by physical removal, burning or killing will stop bulking or growth of the tubers. It will promote the separation of tubers from rhizomes (stolons). Harvest is made easier with less wear on machinery parts. Most importantly, it will reduce the danger of vines spreading pathogens from vines to tubers and reduce disease occurrence in storage. Key diseases of concern are late blight, early blight, bacterial soft rot, viruses such as leaf roll virus causing net necrosis, and others.
Tuber Maturity
For tubers to store well and for processing into chips and fries, they need to mature. Vine kill stops nutrient flow from the vine into the tuber. The skin will set, that is, thicken and harden, thereby reducing bruising such as skinning and shatter. This also reduces the danger of diseases in storage as many pathogens enter tubers through breaks in the skin. With vines dead, the tubers can maintain their dry matter content, such as starch, protein and vitamins, and maintain a sugar (glucose and sucrose) level acceptable for frying to make chips and fries. It takes about three weeks after vine death, depending on conditions, for tuber skins to set and maturation to complete (Pavlista, 2002).
Timing and Conditions
Vine desiccation occurs at the end of the growing season after the log phase of tuber bulking. With fall harvest, that is at the end of August to the end of September or about 14-16 weeks after planting. The soil moisture should be about 65% field capacity and little, if any, irrigation is needed. To avoid soil clumping, sometime some irrigation is given. No fertilization, specifically, nitrogen is desired although some sulfur, as ammonium sulfate or sulfuric acid, application can enhance vine desiccation. Nitrogen application late in the season can delay vine senescence, inhibit desiccation and promote regrowth of new branches.
Reference
- Pavlista, AD. 2002. Skin set evaluation by skin shear measurements. Am Jour Potato Res 79:301-307.
Mechanical Desiccation
There are several methods for mechanically desiccating vines. They each have some advantages but their problems usually outweigh them. One problem that they all have in common is that the vines are removed and death is too quick. A too rapid vine death causes tuber problems such as vascular discoloration.
Beating and Flailing
A vine beater consists of a drum with either chains or flails attached that are hanging down and, while the drum spins, shred the vines. It works best when the lengths vary according to the contours of the rows. Beating and flailing works best when done in combination with chemical vine desiccation, either just before or a week after application.
Advantages -- It is quick and easy, and there are no debris piles.
Problems -- The chains can remove some of the soil, and can hit exposed tubers skinning them. The terrain can affect efficiency. Maintenance can be difficult.
Rolling
A roller consists of a bar with used tires from end to end and dragged behind a tractor. It rolls over vines crushing them.
Advantages -- It is cheap. The field gets smoothed and works well with chemical desiccation.
Problems -- It has one very big problem. By crushing vines, the tires pick up sap from the stems. If the plant is infected, whether it is a virus such as leaf roll, bacterium such as black leg, or fungus such as late blight, the sap on the tires will spread the pathogens (disease-causing agents) throughout the field causing major problems in storage and with the next year's crop. Also, rolling is relatively ineffective as a desiccation method by itself.
Undercutting
Undercutting involves dragging a metal blade through the row cutting the vine just below the ground. This is an old method, still used in dry bean harvest.
Advantages -- It is cheat and there are few clods produced.
Problems -- The big problem is that if damages tubers near the surface reducing yield and quality. Desiccation may be partial and regrowth of branches is common.
Pulling
Special equipment is used for pulling with which vines are physically pulled out of the ground.
Advantages -- Desiccation begins immediately and complete. Pulling is done easily with the proper equipment. The risk of spreading disease spread is nearly eliminated.
Problems -- The equipment is expensive and is not readily available everywhere. Soil dries as well as the plant possibly causing harvest problems.
Flaming
A flamer is pulled behind a tractor. It carries propane gas which is ignited at the nozzle and literally cooks the vines. The tractor must travel relatively fast to avoid danger to the equipment and operator.
Advantages -- It is fast.
Problems -- It is dangerous and scarry.
Chemical Desiccation
There are several reasons for desiccating vines chemically as opposed to mechanically and there are several products available.
Purposes
Using a chemical product will kill vines, leaves, branches and stem. This makes harvesting much easier and cleaner of debris. Since chemical vine desiccation with the exception of sulfuric acid takes time, usually three weeks, to complete, tuber maturity and skin set has time to develop and complete. Very importantly, this is the best method to control disease spread.
Advantages are that using desiccants stops growth, reduces foliar mass and protects tubers. Bruising does not occur as it often does with mechanical desiccation.
Problems do exist. The major one is consumer fears of potential residue. Chemical desiccation costs more than mechanical. Weather conditions, even time of day of spraying, can cause erratic results.
Common Desiccants
Diquat -- Possibly the most common and effective desiccant used is diquat dibromide, commonly called diquat. Diquat has been successfully used for a number of decades. It is used throughout the world under product names such as Regulone and Diquat. It works best when vines show signs of senescence. On large vines, sometimes two applications, a week apart, is required. Diquat is at times used in conjunction with vine beating. Either, the vine tops are beaten first to eliminate the upper half to two-thirds of the plant and then shortly afterwards diquat is applied. Or, diquat is applied first to kill the leaves and weaken the stem, and then about two weeks later, the vines are beaten to shred any slow dying stems and regrowth.
Paraquat -- A close relative of diquat, paraquat dichlor has been used even longer than diquat. It works somewhat better than diquat when used on younger, growing plants but there have been decay problems with storing potato tubers from vines desiccated with paraquat. This has restricted labeled use of the material.
Endothall / Hydrothol -- Endothall is a mixture of two salts and hydrothol is one of these salts of endothall formulated alone. The product names of this desiccant are Des-I-Cate and Flair, and are more recent chemicals. In Des-I-Cate, ammonium sulfate has been added to increase desiccation effectiveness but in some situations, this may also promote regrowth (Pavlista, 2001).
Sulfuric Acid -- Sulfuric acid, which can be used as a sulfur fertilizer or to acidify alkaline soils, needs to be applied with very specialized equipment. It is dangerous to the applicator and specially licensing is often required. The acid, which has a very low pH in its concentrated form, is applied at high concentrations, around 90%, directly to plants. Sulfuric acid can be used unchanged or as a product that release the acid such as Enquik. Products such as Enquik are not quite as dangerous as straight sulfuric acid. Its advantages are a very quick kill and the ability to kill pathogen spores, especially Phytophthora infestans (late blight), on contact at the soil surface. However, pathogens that are not directly in contact with sulfuric acid, such as being under debris, will not be affected. Sulfuric acid is very short lasting as it will be diluted and neutralized by the soil. The vine kill is so quick that the tubers will not mature nor set skin, and vascular discoloration is common.
Reference
- Pavlista, AD. 2001. Hydrothol as a vine desiccant of 'Atlantic' potatoes. J Vegetable Crop Production 7:59-68.
Section 25(b) Chemicals
Section 25(b) Chemicals
Chemical products containing active and inert ingredients considered minimum risk are registered under Section 25(b) of FIFRA (Federal Insecticide, Fungicide Rodenticide Act). They are NOT required to have an EPA registration number and are exempt from EPA regulations on efficacy and toxicity. The exemption from Federal registration is allowed only if the manufacturer uses approved active and inert ingredients, and follows EPA labeling guidelines. There are 31 approved active ingredients with pesticide claims on the Section 25(b) list and nearly all of them are natural products (Table 1). A pesticide is defined by FIFRA as "(1) any substance or mixture of substances intended for preventing, destroying, repelling, or mitigating any pest, (2) any substance or mixture of substances intended for use as a plant regulator, defoliant, or desiccant, and (3) any nitrogen stabilizer."
(http://www.epa.gov/opppmsdt1/PR_Notices/pr2000-6.pdf).
Products exempted from registering with EPA under Section 25(b) are also exempted from full state registration by the Nebraska Department of Agriculture (NDA). NDA requires that Section 25(b) labels be submitted, reviewed and approved by them prior to sale within the State.
(http://www.agr.state.ne.us/division/bpi/pes/25policy.htm).
Some characteristics of Section 25(b) labels are:
- No approval or review by EPA done.
- Manufacturer is responsible for label content.
- Ingredients are limited to those approved by the EPA.
- No EPA Reg. # issued to identify label.
- No EPA Establishment # is required.
- No signal word is required notifying danger.
- No personal protective equipment (PPE) is required.
- False or leading statements as defined are not allowed.
To growers, a key important point about Section 25(b) products is that the sellers do NOT have to prove efficacy for their claims to either the EPA or the states. An example is a product with the Section 25(b) active ingredients sodium lauryl sulfate @ 0.109%, soybean oil @ 0.0004% and corn oil @ 0.002% plus various "inert ingredients" (99.8%). Sodium lauryl sulfate is a foaming agent refined from coconut oil and found in shampoos. This product is sold as an insecticide, however, demonstrations have shown that this product does not kill insects much. It still can be sold for this use since EPA and state registrations are not concerned with efficacy.
Note that there are products resembling Section 25(b) products in the marketplace that have not received federal and state approval. So a buyer should be aware and wary of unsupported label claims. These products may contain unapproved ingredients. Since they do not contain signal words or requirements for PPE, they could be pose potential health risks. They also may be ineffective, as already noted, and be a waste of money.
(source: Schulze, L. 2003. The Label v.15,i.11.)
Table 1. Active Ingredients under Section 25(b) FIFRA
- Castor Oil
- Cedar Oil
- Cinnamon and Cinnamon Oil
- Citric Acid
- Citronella and Citronella Oil
- Cloves and Clove Oil
- Corn Gluten Meal
- Corn Oil
- Cottonseed Oil
- Dried Blood
- Eugenol
- Garlic and Garlic Oil
- Geraniol
- Geranium Oil
- Lauryl Sulfate
- Lemon grass Oil
- Linseed Oil
- Malic Acid
- Mint and Mint Oil
- Peppermint and Peppermint Oil
- 2-phenylethyl propionate
- Potassium Sorbate
- Putrescent Whole Egg Solids
- Rosemary and Rosemary Oil
- Sesame (includes ground Sesame plant stalks) and Sesame Oil
- Sodium Chloride (common salt)
- Sodium Lauryl Sulfate
- Soybean Oil
- Thyme and Thyme Oil
- White Pepper
- Zinc Metal Strips
Section 25(b) Regulation: The Text
May 7, 2000
PESTICIDE REGISTRATION (PR) NOTICE 2000-6
NOTICE TO MANUFACTURERS, FORMULATORS, PRODUCERS AND
REGISTRANTS OF PESTICIDE PRODUCTS
ATTENTION: Persons Responsible for Registration of Pesticide Products
SUBJECT: Minimum Risk Pesticides Exempted under FIFRA Section 25(b)
Clarification of Issues
I. PURPOSE
This notice clarifies several aspects of the exemption for minimum risk pesticides by the FIFRA Section 25(b) rule, including composition, labeling, food tolerances, and state regulation. It is being issued to answer questions frequently asked of EPA about such products.
II. BACKGROUND
Section 2(u) of FIFRA defines a “pesticide” as “(1) any substance or mixture of substances intended for preventing, destroying, repelling, or mitigating any pest, (2) any substance or mixture of substances intended for use as a plant regulator, defoliant, or desiccant, and (3) any nitrogen stabilizer.” Except in very limited circumstances, any substance falling within this definition of a pesticide must be registered by EPA before it can be legally sold or distributed. One such exception to the registration requirement is for those pesticides that the Administrator, under section 25(b) of FIFRA, has determined “to be of a character which is unnecessary to be subject to this Act,” and that have been exempted from the requirements of FIFRA by regulation. In 1996, EPA exempted certain minimum risk pesticides from FIFRA requirements if they satisfy certain conditions. EPA exempted the products described in 40 CFR section 152.25(g) in part to reduce the cost and regulatory burdens on businesses as well as the public for pesticides posing little or no risk, and to focus EPA’s limited resources on pesticides which pose greater risk to humans and the environment. This exemption provision is located in section 152.25(g) of Title 40 of the Code of Federal Regulations.
To qualify for an exemption as a minimum risk pesticide, each active ingredient in the pesticide product must be listed in 40 CFR 152.25(g)(1). Appendix A is a list of these ingredients. Currently, this list contains more than 30 active ingredients. In addition, 40 CFR
152.25(g)(2) provides that these pesticide products may only contain minimal risk inert ingredients listed in the most current List 4A. Appendix B is the most current list of these inert ingredients. Additionally, to be exempted and remain exempted, products must also meet a series of exemption conditions described in 40 CFR 152.25(g)(3).
(Please Note: List 4A, "Minimal Risk Inerts" (Appendix B of this notice) is updated on a continuing basis. Current versions are available on the Pesticides Web site at http://www.epa.gov/opprd001/inerts/inerts_list4.pdf.)
EPA does not review or issue notices of exemption for products which meet the conditions for exemption. Sale or distribution of a pesticide product meeting all the criteria in 40 CFR 152.25(g) without a federal registration is not a violation of FIFRA. However, if a product does not meet all of the exemption criteria, the product is not exempt from FIFRA and its sale or distribution if not registered would be a violation of FIFRA.
How to Determine if a Product Qualifies for Exemption as a Minimum Risk Pesticide Under 40 CFR 152.25(g).
QUESTION: How can I tell if my product qualifies for the minimum risk pesticide exemption?
ANSWER: To qualify as a minimum risk pesticide under 40 CFR 152.25(g) (and be exempt from pesticide registration), a product must meet certain conditions. These conditions fall into the following two categories.
1. Composition:
• active ingredients: may contain only those active ingredients that are listed in 40 CFR 152.25(g)(1) and shown in Appendix A.
• other (inert) ingredients: may contain only List 4A inerts, including commonly consumed foods. (See Appendix B).
2. Labeling:
• All ingredients in an exempted product must be listed on its label:
- Active ingredients must be listed by name and percentage (by weight).
- All other ingredients must be listed by name (see above for inerts).
• No false or misleading statements under 40 CFR 156.10 (a)(5)(i)-(viii) may appear on an exempted product’s label.
• Labeled Uses:
The product may not bear any claims to control or mitigate microorganisms in a way that links the microorganism to a threat to human health (including but not limited to disease transmitting bacteria or viruses) or claims to control rodent or insect pests in a way that links the pest to specific diseases (for example, the label may not say "controls ticks that carry Lyme disease" or "controls mosquitoes that can transmit malaria or encephalitis," but can say “controls ticks,” or, “controls mosquitoes,” etc.). It is important to note that even if a pesticide product meets the conditions for exemption from regulation under FIFRA, it is still subject to any applicable requirements of the Federal Food, Drug, and Cosmetic Act (FFDCA) if its use results in pesticide chemical residues on or in food commodities or animal feed. In addition, producers of pesticides must meet any applicable state registration or other regulatory requirements. Each state has its own statutes and regulations concerning pesticide registration and regulation, and the states are not required to permit the sale of an exempted product simply because it meets the 40 CFR 152.25(g) conditions for minimum risk exemption. An address and telephone list of the state agencies which regulate pesticides may be found at: http://aapco.ceris.purdue.edu and at
http://www.epa.gov/pesticides/biopesticides/otherdocs/statelist.htm. You may also call (703) 305-7973 to obtain a paper copy.
III. COMPOSITION OF "MINIMUM RISK PESTICIDES"
1. Active Ingredients
QUESTION: What active ingredients may be used in an exempted pesticide product?
ANSWER: Only active ingredients listed in 40 CFR 152.25(g)(1) may be in exempt products. Appendix A to this PR Notice lists all of the active ingredients which are currently permissible ingredients in exempt products.
QUESTION: Can other active ingredients be added to this list? How?
ANSWER: The Agency may modify this list in the future, but any additions (or deletions) would have to be accomplished through rule making. Companies cannot obtain an exemption on an ad hoc basis as part of the application process. EPA cannot exempt an ingredient or product as part of the application process without having completed the required rule making.
2. Other Ingredients
QUESTION: What other ingredients may be used in exempted products?
ANSWER: The only other ingredients an exempt product may contain are listed in the most current List 4A inert ingredients, which the Agency last published in the Federal Register of September 28, 1994. List 4A inert ingredients are considered to be minimal risk inert ingredients, and are recognized as safe for use in pesticide products. The current List 4A minimal risk inerts are listed in Appendix B to this PR Notice.
QUESTION: Can common foods be used as inert ingredients in exempted products?
ANSWER: Yes. EPA's policy is that "commonly consumed foods" are considered List 4A inerts of minimal concern, even if they are not already included on the list of minimal risk inerts. (See 59 FR 49400, September 28, 1994) “Inert Ingredients in Pesticide Products; List of Minimal Risk Inerts.”
QUESTION: Will additions to the List 4A be possible?
ANSWER: Yes. Additions to List 4A are being considered by the Agency. Any changes will be published in the Federal Register.
QUESTION: If a List 4A minimal risk inert has active, pesticidal properties, am I allowed to use it as the active ingredient in an exempt product?
ANSWER: No. The two lists are not interchangeable. In other words, you may not use a List 4A inert ingredient as an active ingredient, and you also may not use one of the active ingredients listed in 40 CFR part 152.25(g)(1) as an inert. Only if the ingredient is included on both lists can it be used without regard to its active or inert function. Even then, the ingredient must be designated on the label as either active or inert (See Labeling below).
IV. LABELING OF MINIMUM RISK PESTICIDES
QUESTION: What should I include on my product’s label?
ANSWER: In order to qualify for the minimum risk pesticide exemption, the pesticide product must meet certain labeling conditions. These conditions, all of which must be met in order to qualify for exemption, are as follows:
1. The pesticide product containing permissible substances must bear a label identifying the name and percentage (by weight) of each active ingredient and the name of each inert ingredient;
2. The product may not bear any claims to control or mitigate microorganisms in a way that links the microorganisms to a threat to human health (including but not limited to disease transmitting bacteria or viruses) or claims to control rodent or insect pests in a way that links the pest to specific diseases (for example, the label may not say "controls ticks that carry Lyme disease" or "controls mosquitoes that can transmit malaria or encephalitis," but can say “controls ticks,” or, “controls mosquitoes,” etc.);
and
3. The product must not include any false or misleading labeling statements prohibited by 40 CFR 156.10 (a)(5) (i)-(viii). To follow is a list of unacceptable types of statements that Agency regulations provide are false or misleading, along with some examples:
a. A false or misleading statement concerning the composition of the product;
b. A false or misleading statement concerning the effectiveness of the product as a pesticide or device;
c. A false or misleading statement about the value of the product for purposes other than as a pesticide or device;
d. A false or misleading comparison with other pesticides or devices;
e. Any statement directly or indirectly implying that the pesticide or device is recommended or endorsed by any agency of the Federal Government;
Example: “Recommended by EPA as safe and exempt.” This kind of statement leads the consumer to believe that the Federal Government has made such a determination for a particular product. Because exempted products are not reviewed by EPA, this kind of statement is misleading.
Example: “It is a Violation of Federal Law to Use this Product in a Manner Inconsistent with its Labeling.”
Example: “EPA Registration No.” or “EPA Establishment No.” The latter two examples are false or misleading because they imply that the product is registered by EPA.
Example: An example of a statement that the Agency would likely consider acceptable would be: “This product has not been registered by the United States Environmental Protection Agency. [The name of the company] represents that this product qualifies for exemption from registration under the Federal Insecticide, Fungicide, and Rodenticide Act.”
f. The name of a pesticide which contains two or more principal active ingredients if the name suggests one or more, but not all such principal active ingredients, even though the names of the other ingredients are stated elsewhere in the labeling;
g. A true statement used in such a way as to give a false or misleading impression to the purchaser;
h. Label disclaimers which negate or detract from labeling statements required under the act and these regulations, including as conditions of exemption.
QUESTION: I have found mosquito and tick repellents on the market shelf that do not have EPA registration numbers. I thought that exempted pesticide products could not be labeled to control these kinds of pests?
ANSWER: Claims that the exempted pesticide controls these kinds of pests are allowed, but no claims may be made to make the consumer believe that they would be protected by using the product from a disease that these insects can carry, such as Lyme disease. Remember: the claim may only be for the pest, as a pest, and not as a disease vector.
Example of an appropriate claim: “repels mosquitoes and ticks.”
Examples of an inappropriate claim: “repels mosquitoes that can transmit malaria,”or, "Will repel ticks that cause Lyme disease."
QUESTION: I have seen products that say they are "the natural way to control pests," or "safe for kids and pets." Aren't these considered by EPA to be false and misleading claims?
ANSWER: No, not for exempted minimum risk pesticides. Products that meet the criteria for exemption from regulation may make safety claims if true. On the other hand, claims cannot be worded in such a way that implies or states endorsement by EPA or another federal agency or department.
V. FOOD TOLERANCES FOR "MINIMUM RISK PESTICIDES"
QUESTION: What are the requirements if my product is to be used on or around food, food crops, food contact surfaces, or animal feed?
ANSWER: Even if a product is exempt under FIFRA, it must have a tolerance or tolerance exemption under FFDCA, if the product is to be used on food, food crops, food contact surfaces, or animal feed commodities.
The minimum risk pesticide exemption, 40 CFR 152.25(g), only exempts qualifying pesticide products from certain requirements of FIFRA. The use of pesticides on food, food crops, food contact surfaces, and animal feed can result in residues of pesticide products on or in treated foods or foods which come into contact with treated surfaces. Tolerances are maximum legally permissible levels of pesticide residues, including active and inert ingredients, which may be found in foods. In some instances, pesticides are exempted from the requirement of a tolerance, because the pesticide is considered to be safe enough for use at any level. Tolerances and exemptions from tolerance are established and regulated by the EPA under the Federal Food, Drug and Cosmetic Act (FFDCA), not FIFRA. The pesticide label may bear only those food uses for which there are tolerances or exemptions from tolerances for the active and inert ingredients. If the tolerance exemption is for all food commodities, then any food crops, food surfaces, or animal feed can be listed on the label.
QUESTION: How can I find out if my active and inert ingredients have tolerances or are exempt from the requirement of a tolerance?
ANSWER: Tolerances and exemptions for foods are listed in Parts 180, 185, and 186 of Title 40 of the Code of Federal Regulations for each active ingredient and inert ingredient. Appendices A and B can be used to identify which actives and inerts are exempt from tolerances on all crops as of the date of this notice. In addition, tolerances and exemptions are published throughout the year in the Federal Register. This source is frequently more up-todate than the latest version of 40 CFR and thus, needs to be checked to verify that no changes have occurred since the last printing of the 40 CFR.
QUESTION: How do I get a tolerance if I need one?
ANSWER: The first step to receive a tolerance is to petition the Agency by following the guidelines found in 40 CFR section 180.7 (see www.gpo.gov). Additional guidance can be found at www.epa.gov/PesticideApplication. The Agency will then announce the receipt of the petition in the Federal register. Tolerance fees are required, but may be waived on a case-bycase basis.
VI. STATE REGULATION OF "MINIMUM RISK PESTICIDE" PRODUCTS
QUESTION: What must I do to meet any applicable state registration requirements?
ANSWER: Even if a pesticide product is exempt from FIFRA requirements, the product may not be exempt from state registration or other regulatory requirements. Each state has its own statutes and regulations concerning pesticide registration and regulation. A pesticide product exempted from federal regulation is not automatically exempt in a state. It is important that you contact the state agencies responsible for pesticide regulation in those states in which you would like to sell your product, so you can find out what you need to do in order to satisfy their requirements for pesticide registration if required. An address and telephone list of the state agencies which regulate pesticides is available online http://www.epa.gov/pesticides/biopesticides/otherdocs/statelist.htm.
You may also call (703) 305-7973 to obtain a paper copy.
QUESTION: What happens if a state won’t accept my product as an exempted pesticide?
ANSWER: You may:
1. Comply with the State’s requirements in order to sell and distribute the product; or
2. Not sell or distribute the product in that state; or
3. You may register the product with the EPA if EPA determines that your product meets all the health and safety standards and all other applicable requirements. You must also meet any applicable State requirements for your product.
If a pesticide product does not meet the conditions for minimum risk pesticide exemption, or if states will not accept the product without an EPA registration, a registration kit may be obtained by calling 703-305-6549. The kit is also available on our website, at www.epa.gov/pesticides/registrationkit.
Please note that the sale or distribution of a pesticide without an EPA registration that does not meet the conditions for a minimum risk pesticide and does not fall within any other exemption from FIFRA is a violation of FIFRA. (See, e.g., FIFRA section 12(a)(1).)
VII. FOR FURTHER INFORMATION
If you have any further questions, please contact the Director Office of Pesticide Programs.
Wonder Products
Agriculture 'Wonder' Products
Wonder products are seldom worthless but usually are not worth their cost for the effect that they may or may not have. Often they are sold with scientific sounding promotion and promise incredible benefits that are not directly substantiated. A typical promoted effects is a reduction of fertilizer application. However, soil fertility is often high in potato crop land, and fertilizer application can be reduced even without the wonder product. Another pitch similar to the old "snake oils" is that the product is a "cure all' for practically all soils and crops. Advertising and sales are usually built entirely on testimonials or anecdotes. Actual, objective data supporting the claims are lacking or taken out of context. Often claims of results are based on visual observations showing an obvious effect of the product. In my experience, this has occurred when the ingredients of the product are not disclosed but the odor clearly indicated the presence of urea which is known to cause a temporary greening of foliage.
So, beware of products claiming:
- Increased soil water-holding capacity,
- Increased soil aeration,
- Increased nutrient-holding capacity or availability,
- Improved soil structure or stability,
- Increased microbial activity,
- Improved uptake of organic matter,
- Increased pest resistance,
- Increased water penetration,
- Improved water-use efficiency or lower evaporation,
- Improved root respiration,
- etc.
Types of Wonder Products:
Soil additives are claimed to reduce or supplement fertilization. Often they contain trace elements and report the total amount present. This may not indicate their availability to the plant, and the soil often naturally has more of the elements then the product.
Soil amendments are claimed to improve the physical or chemical properties of the soil. Changing soil structure, soil texture, pore capacity, aeration, or water-holding capacity is just about impossible and would require massive amounts of amendments. A simple and not uncommon example is lowering soil pH with tons of elemental sulfur per acre. Adding even several pounds would make an infinitesimal change.
Microbial inoculants supposedly increase populations or stimulate activity. The amount of contribution of these inoculants is infinitesimal compared to the actual natural population already in the soil. Some products were pasteurized for shipping and handling, and so any organisms are actually dead. Note: these products should not be confused with nitrogen-fixing bacteria, Rhizobia spp., used in legume agriculture which are well-documented in science.
Soil humus, humic acid and fulvic acid are terms used for mineral organic matter products and are classed as humates. They are claimed to increase soil levels and activity of soil organic matter. Soil humus is composed of a lot of compounds ranging from known biochemicals to polyelectrolytes resulting from dead microbes. These products would have little effect on the soil. For example, soil containing 3% organic matter has 60,000 lb organic matter per acre at furrow depth. Adding 500 lb of a commercial humate containing 60% organic matter will increase the soil's organic content to 3.03%.
Plant growth regulators (PGR) are well documented to affect plant growth and many are natural hormones found in the plant. They can have both a beneficial and a harmful affect on plants depending on dose and application timing. Examples are gibberellic acid for potato sprout promotion, maleic hydrazide for sprout inhibition, and 2,4-D for weed control. Some wonder products may contain some real PGRs. However, PGRs have very defined specific uses and applying them to the soil is NOT one of them. In 40 years of research on PGRs, I have never come across one or combination of PGRs that is active when applied to the soil. To have an effect, PGRs need to be applied to living plant tissue, seed, tuber, stem, leaves, root, flower, fruit, etc. Examples of PGRs in agriculture are auxins such as 2,4-D and dicamba, cytokinins such as kinetin, gibberellins such as gibberellic acid (GA3), and ethylene, a gas.
Wonder products or "soil medicines" can not ever substitute or supplement good agronomic practices. So, buyer beware.
Reference: McDole, R.E. and C.G. Painter. 1979. Wonder Products in Agriculture. U. Idaho CIS #510.
Perception of Risk
Pesticides and Perception of Risk
Are natural products safer than synthetic ones? This is a fundamental question that has been asked by faculty who have reviewed the scientific literature such as Dr. Joel Coats of Department of Entomology at Iowa State University. It is a difficult question to pose and analyze, but such as needed to clarify some of the confusion over the assessment of risk.
The experience of the general public on controlling pests is limited to their house, yard, garden, and pets. Urban situations account for at least a quarter of all insecticides used. Consumers seem to have a wide acceptance of pesticides as long as they are the ones using them regardless of the fact that they are not professionals. The same people may indicate a distrust when these materials are in the hands of others even though they may be trained and licensed, and aware of the label regulations. There are also other factors that contribute to this distrust.
Most chemicals registered as pesticides are lab-synthesized, petroleum-based ingredients. Distrust of synthetic insecticides began in 1962 when the press featured stories about DDT contaminating fish causing fish-eating predator populations to decline as a result of thin egg shells. Later insecticides were the organo-phosphates and carbamate esters that were more biodegradable but had broad-spectrum toxicity and could affect non-target organisms. Some were highly target-specific and very safe such as carbaryl (Sevin) used in gardens and in flea collars for cats and dogs.
Most people do not understand pesticide products and therefor are uncomfortable with their use in food supplies. For instance, inhaling benzene fumes while filling up the car with gasoline poses a much greater health risk than irradiating food or administering growth hormones to cows. But, people are familiar with filling up their car with gasoline and the use of gasoline. They do not understand the actions of pesticides or appreciate their use very well.
The general public feels that they are far removed from the decision-making process that registers products or control of their exposure to them. Their experience with exposure is primarily due to mis-applications such as herbicide drift on the lawn, yard or garden or to bodily reactions because they spilled the concentrated product or sprayed it on themselves unintentionally. Interestingly germicidal pesticides, fungal ointments and bug repellents are widely accepted. But, again these are more familiar and their purpose clearer to the public. Also exposure is usually voluntary.
The public is also suspicious that not all the effects of chronic, long-term exposure are known. There are a few cases where this may have happened. For instance, it took many years for the environmental effects of chlorinated hydrocarbons to be fully understood. These cases are rare but not unique to agricultural chemical. Common and serious examples are lead in paint, recently re-appearing on children's toys from China, and asbestos in school buildings.
Surveys showed that just about every household in this country used some pesticide product within a year. Many homes are treated every year by pest control operators and yards treated by lawn care outfits. Pesticide products are applied with care, following labeled instructions, and few accidents occur. Factors that are responsible for the most deaths in this country, over 10,000 per year, are tobacco, alcohol, cars, murder, and falls. Of poisonings, pesticides accounted for 12 possible cases in 1988.
People often respond to risk irrationally, that is, not in agreement with statistical records on likelihood of hazard occurrence. One measure of risk used by governments is the chance of dying in any year of one individual out of a million. Under this measure, you would have a one in a million chance of dying in the coming year by traveling on a bicycle for 10 miles, in a car for 150 miles or in a jet plane for 3,500 miles, or even canoeing for six minutes. The same is true if you eat 40 tablespoons of peanut butter or have a chest X-ray. Surgery, X-rays and alcohol use are much more dangerous than pesticides, police work or privately flying a plane, however the public believes the opposite to be true. Risks are perceived based on low familiarity and high dread.
Chemicals synthesized in the laboratory or found in nature, such as glycoalkaloids, some can be hazardous and some safe. Some may be toxic and some not, and some may leave residue and some may not. Three significant conclusions can be discerned:
1. The biological activity of a chemical depends on its structure regardless of source.
2. Safety depends on the chemical structure and the way the chemical is used.
3. Perceived risk is often not consistent with actual risk but related to familiarity.
References:
- Facts Versus Fears: A Review of the Greatest Unfounded Health Scares of Recent Times. 1998. by Lieberman, A.J. and Kwon, S.C., publ. American Council on Science and Health, NY, NY
- Coats, J.R. 1994. Risks from natural versus synthetic insecticides. Annual Review of Entomology 39:489-515. (source: Schulze, L. 1994. The Label v.6,i.5.)
Chemophobia
Dealing with Chemophobia
Several agrichemical companies established a Consumer Information Program to deal with the public's fear about agrichemicals. This program conducted a survey on the public's perceptions on pesticides. Cancer was concern #1. There was a desire for organic farming to increase and felt that the technology was available but ignored by farmers. One outcome of this survey was to determine what information may ease the public's anxieties and what information does not.
Statements that help relieve chemophobia concerning pesticides:
Pesticides undergo a rigorous testing process. There are more than 120 separate tests taking 8-10 years at a cost of $35-50 million that must be passed.
Only about one in 20,000 compounds make it to the farm. Monitoring of agrichemicals continues even after chemical registration.
The National Cancer Institute has stated that there is NO scientific evidence that pesticide residues on produce causes cancer in people.
A 40-lb child would need to eat 340 oranges each day for a lifetime and still would not consume enough pesticide residue that would cause a health problem in a mouse.
People's confidence in pesticides was greatly increased when they learned about the amount of initial and ongoing testing performed on each chemical. Most people do not know or understand the strict regulatory criteria used on pesticides. An explanation of these requirements gives more confidence in how a chemical gets to the agricultural market.
Arguments that do not help relieve the public's concern:
Risk comparisons such as one in a million aren't effective. It implies that a person could be that one and note there are 8 million people in New York City and in Los Angeles. The world needs to be fed and pesticides are an integral part of farming does not work. There are far more naturally-occurring chemicals that are really dangerous such as cyanide, strychnine and many natural carcinogens. The public assumes that people can break these down, metabolize, in the body system since we live with these chemicals. The fact that organic food supplies have serious drawbacks doesn't help. It's better to explain integrated pest management (IPM) and sustainable agriculture.
[adapted from "Pesticide Notes" published by Michigan State Univ.]
How Gullible Are We?
In 1998, Nathan Zohner, then a freshman at Eagle Rock Junior High School in Idaho Falls, ID, decided to show how conditioned people had become to alarmists practicing junk science. For his science project for the Greater Idaho Falls Chamber of Commerce, he urged people to sign a petition demanding strict control or total elimination of the chemical “dihydrogen monoxide.” He told those who signed that:
It caused excessive sweating and vomiting.
It is a major component in acid rain.
It can cause severe burns in its gaseous state.
Accidental inhalation can kill you.
It contributes to erosion.
It decreases effectiveness of car brakes.
It has been found in tumors of cancer patients.
He asked 50 people if they supported a ban of this chemical. Forty-three said yes, six were undecided, and only one knew that dihydrogen monoxide was actually water.
The title of his prize-winning project? “How Gullible Are We?”
[taken from the “Potato Grower, vol. 27, iss. 2, Feb. 1998.]
Lab to Label
Lab to Label
People in general have a poor concept of what it takes to bring an agricultural product to the farm. Many have misconceptions concerning toxicological and environmental testing, and government regulations and requirements. Only about one in 20,000 compounds pass testing from synthesis to field use. It undergoes some 120 separate toxicological and environmental tests, ensuring that the compound poses no health or environmental concerns when used properly. Product development, testing and approval by the EPA takes from eight to 10 years and costs over $50 million (1990). This also leaves only about seven to nine years on the patent for the developer to recoup the costs.
Because of the importance for people to understand this process, this is the first part of a multi-part article on the general scheme for taking a compound out of a test tube to the crop. The article is based on my decade-long experience as a researcher in a chemical company and a brochure called "from Lab to Label" published by the American Crop Protection Association.
Phase I. Screening (Discovery)
Primary Screening
Small quantities, as little as an ounce, of a compound is synthesized. The compound may be a derivative of another compound, an analog, or a foray into a new chemical sequence, or a by-product of a methodology used for something else, commonly a fermentation by-product. (The latter is the reason why most large ag-chemical manufacturers are closely related to a pharmaceutical manufacturer, such as Bayer.) In a large ag-chemical company 10 to 20 thousand compounds are made each year; exact numbers are kept confidential.
These compounds are tested routinely in special laboratory and greenhouse tests developed by the company's researchers. They are tested in these mini-screens for activity. The protocols for these tests are kept under trade secrets and change according to market development and interest.
After this initial screening, 100 to 500 of the 10-20,000 show some interesting activity warranting further testing in the greenhouse or insectary, etc. At this point, the first toxicological tests kick in. The most important and immediate test is the Ames mutagenicity test. This laboratory test on bacteria looks to see if the compound can alter DNA, normally by base substitution, and results are back in a few days. If it does, it's finished and will never leave the lab. The only testing permitted is by company researchers under highly protective conditions in the lab. This limited testing may be done by the researcher for various reasons, usually to define structure-activity relationships and look for non-mutagenic analogs.
If the compound passes this test, it will undergo an eye irritation test with a rabbit. This is a mild test and used as a guide for applicators. If the compounds might be tested other than locally at the research and development center, it must go through both oral and dermal toxicity tests on mice. This will determine the compounds LD50 or what is the dose for 50% mouse mortality when the compound is ingested or in skin contact. If the LD50s are acceptable, it is cleared for shipping in sealed packages.
Secondary Screen
About 100 to 500 compound per year are retested in the laboratory and greenhouse. These tests are designed to determine active rates and application timings, and determine the target pest and crop. Compound may be tested several times before going to the field for testing. Compounds that look promising are re-synthesized in slightly large quantities, 1 to 5 ounces.
Tertiary Screen
This is the first field screening of compounds. Of the compounds tested in the secondary screen, 10 to 60 compounds will undergo small scale field tests. These tests are conducted initially on company research farms and are conducted in small plots. Application timing and method, rates, and some structure/activity tests are conducted. Analogs of active compounds are synthesized and tested in the secondary screens for activity and patent purposes. All of these analogs are also tested in the mutagenicity test and active ones are further put through the eye irritation, dermal toxicity and oral toxicity tests. From the initial field test, a few compounds, less than 10, are sent for testing by a few University researchers around the country in small plot evaluations to confirm the company's research and to determine activity in a wider range of situation.
At this time, the selected compounds undergo formulation testing. Formulation testing looks at different carriers and physical properties of the compounds. University researchers get test compounds in a preliminary formulation, usually a liquid flowable (LF), emulsifiable concentrate (EC) or wettable powder (WP). This is quite different than the form in the primary and secondary screens in which the compound is unformulated and tested in a solvent such as acetone.
At the same time, environmental impact testing begins on compounds going into tertiary screening. The compound's persistence in different soils and breakdown by soil microbes are key tests. Its volatilization and solar effects are measured. How it is metabolized by both the target crops and pests are determined using radio labeled tagging. The method of uptake, for instance root or foliar, and percent penetration and translocation are determined.
Toxicological testing is expanded to determine speed and amount mice excrete the compound, urine and feces. The metabolic breakdown of the compound in mice is determined, and all metabolic products are identified. These are called the "7-day toxicology studies" and a problem here, such as the formation of a dangerous by-product in the mouse, would eliminate the compound and possibly the whole chemistry from further testing.
In summary Phase II testing involves field efficacy trials, preliminary formulation studies, environmental persistence determinations, plant and/or pest metabolism, and rodent excretion and metabolism.
Of the 10-20,000 compounds that are screened each year (Phase I), only one to six go into Phase II Development.
Lab to Label: