An off-the-shelf data acquisition tool and new tractor technologies are helping a University of Nebraska researcher more precisely characterize power use with today’s tractors and implements. This analysis could lead to increased field efficiency and improved energy and fuel use for producers. Typically, fuel use accounts for approximately 3%-5% of field production costs.
“Five years ago we couldn’t easily collect this data on tractor performance, but now tractors have communication ports,” said Santosh Pitla, assistant professor of advanced machinery systems in the Department of Biological Systems Engineering at the University of Nebraska in Lincoln.
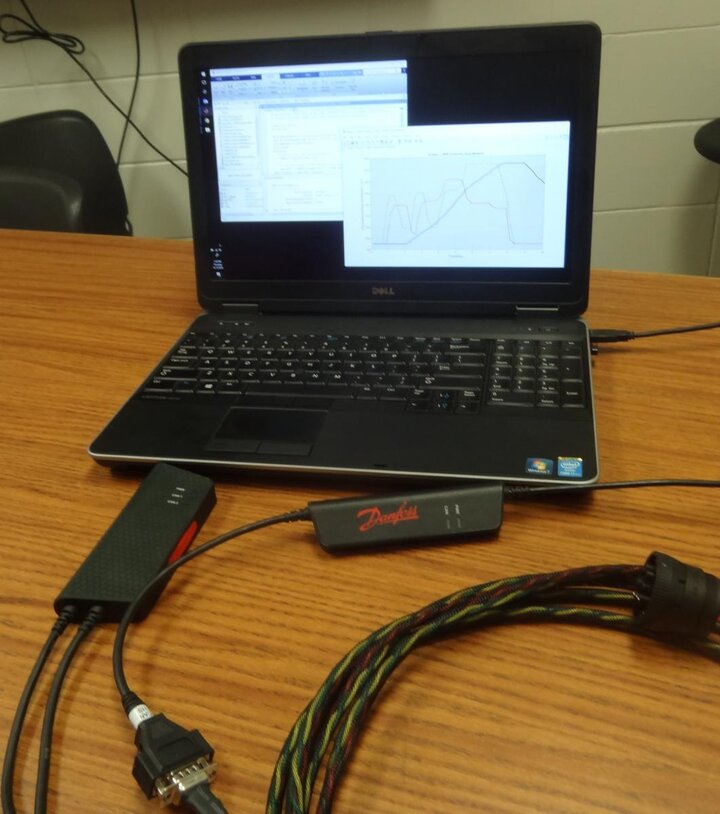
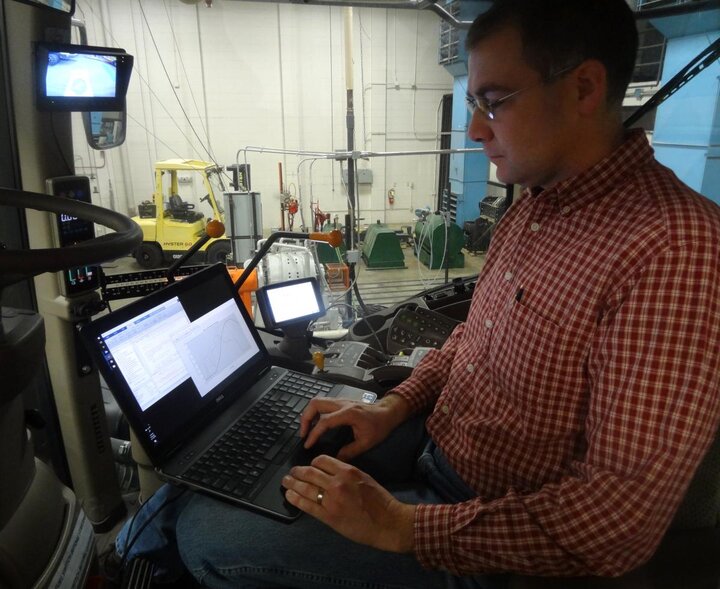
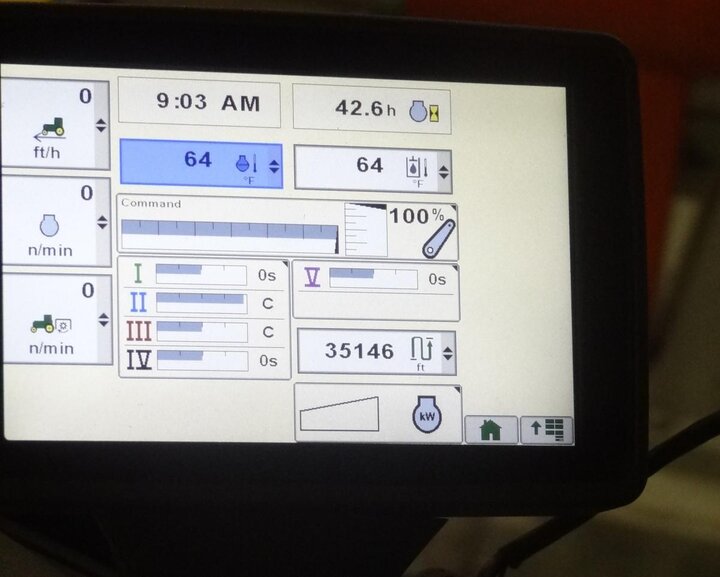
These ports, like those on cars, are designed to provide diagnostic and performance data. A commercially available “plug-in” tool is used to download this data from the tractor. The software that Pitla is developing then takes this information a step further to more precisely analyze power use under various conditions and practices in the field.
“In a couple of years, after testing, programming, and studying multiple producers and tractors, we hope to have enough data to have the true load cycles of the tractors,” said Pitla.
Every tractor now has multiple computers — some as many as 20 — and they all talk via a common language accessed via the Controller Area Network (CAN). Using CAN data, Pitla is studying information from the main engine and implement controllers to characterize how power use changes during different operations and for specific field conditions.
“With this technology, we can be very specific,” Pitla said. “Fields vary in shape, slope, waterways and other attributes. You might be running at 80% efficiency in Field A and 70% in Field B.” Knowing the field-specific differences and how they affect energy use can lead to good management practices and improved operational behavior related to fuel use rate, torque, and engine rpm, Pitla said.
“In calculating load, we’ve been relying on equations developed 50-70 years ago. Draft for today’s planters is much different. Today’s tractors have GPS and increased electrical needs.”
Identifying Actual Power Needs
How much of your engine is actually utilized? How much tractor power do you need? By analyzing operational data specific to a given farm, a producer might learn that their tractor is oversized and only 60% of its power is being used.
“We don’t necessarily know how much power a 12-row planter needs. With this technology, we can be very specific in making recommendations on how to operate the machinery to optimize efficiency.”
For example, the power requirements are significantly different for a central fill planter compared to a row fill planter, Pitla said. “The central fill requires a hydraulic motor and central power from the tractor, using approximately 30-40 hp.”
This information could also be applied to equipment selection and matching the power needs of current and potential uses with that of tractors being considered for purchase.
Field Testing
After several years of university development, the data acquisition system is now being tested in farmer fields. Among the testers is Kerry McPheeters of Gothenburg, a recent UNL mechanized agriculture graduate, who is using it with his brother Clark McPheeters on their family farm for operations such as planting, field cultivation, and harvesting.
The data acquisition tool will also be tested at the Nebraska Tractor Test Lab on UNL’s East Campus, the only US tractor testing station for the Organization of Economic Co-operation and Development. Roger Hoy, director of the Nebraska Tractor Test Lab, and Rodney Rohrer, NTTL research engineer, previously worked on the Agricultural Industry Benchmark Study for Reduction in Petroleum Use. They will add tremendous insight into the current research efforts, Santosh said.
Joe Luck, assistant professor, Mike Kocher, associate professor, John Evans, graduate student, all in the Department of Biological Systems Engineering, are collaborating with Pitla on the tractor machine data acquisition work. Pitla and Evans are teaching a special topics class this semester to train agricultural engineering students on CAN-based embedded controller systems, preparing them for industry. Leading CAN automation industry partners, Danfoss Power Solutions and Kvaser Inc., are supporting these research and teaching activities.
Moving from the Lab to the Cab
Eventually, Pitla hopes to develop a program that could be used in the cab or from a smart phone to analyze data on the go, giving almost immediate feedback to support in-field adjustments to optimize energy/fuel consumption and field efficiency. This could be especially helpful to young producers — like having a mentor sitting at their side in the cab suggesting when to slow down or adjust operations.
In addition to his research, Pitla teaches mechanized agriculture for agricultural engineering students and leads the Advanced Machinery Systems Lab in the UNL Department of Biological Systems Engineering. Earlier this year Pitla was awarded the Sunkist Young Designer award from the American Society of Agricultural and Biological Engineers for innovative automation and robotics engineering design contributions for agricultural applications in academia and industry.
Resources
Further information on CAN tools and data analytics research can be found in the following articles:
- Pitla, S.K., J.D. Luck, J. Werner, N. Lin, and S.A Shearer. 2016. In-field fuel use and load states of agricultural field machinery. Computers and Electronics in Agriculture 121: 290 - 300.
- Pitla, S.K., N. Lin, S.A. Shearer, and J.D. Luck.2015. Use of Controller Area Network (CAN) data to determine field efficiencies of agricultural machinery. Applied Engineering in Agriculture. Vol. 30(6): 829-839.
- Marx, S.E., J.D. Luck, S.K. Pitla, R.M. Hoy. Comparing various hardware/software solutions and conversion methods for Controller Area Network (CAN) bus data collection. Computers and Electronics in Agriculture 128:141-148
- Marx, S.E., J.D. Luck, R.M. Hoy, S.K. Pitla, M.J. Darr, and E. Blankenship. 2015. Validation of machine CAN Bus J1939 fuel rate accuracy using Nebraska Tractor Test Laboratory fuel rate data.Computers and Electronics in Agriculture 118: 179-185.
- Hoy, Roger, Rodney Rohrer, Adam Liska, Joe Luck, Loren Isom, Deepak Keshwani. University of Nebraska–Lincoln, Department of Biological Systems Engineering, Nebraska Tractor Test Laboratory September 2014. Agricultural Industry Advanced Vehicle Technology: Benchmark Study for Reduction in Petroleum Use